info
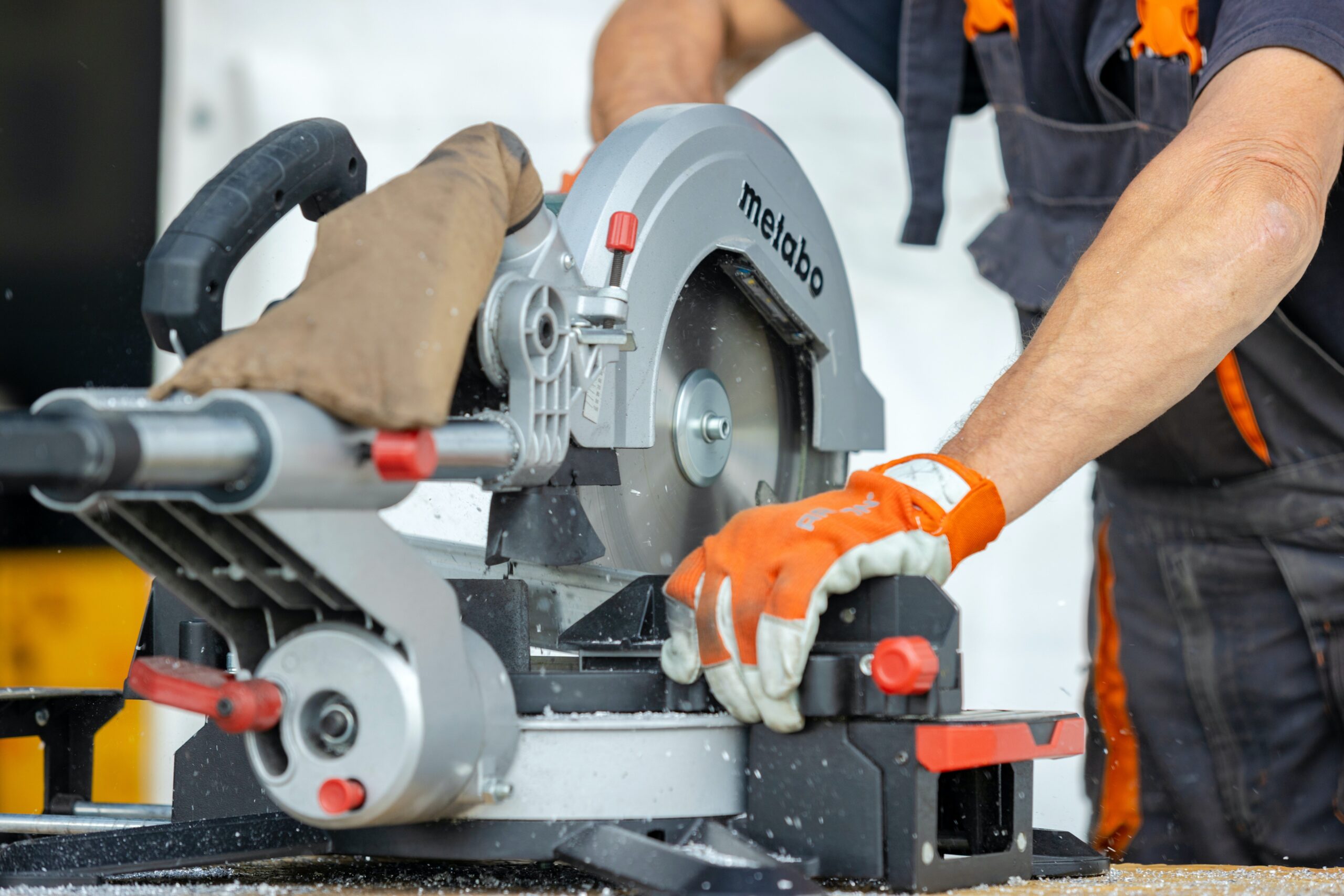
Importance Of Portable Appliance Testing
Portable Appliance Testing (test & tag) is recommended by Worksafe and demonstrates a duty of care to the people who work in and visit your premises. Testing and tagging is one way to minimize the risk of an electrical accident in your workplace.
Under the Victorian Occupational Health and Safety Act (2004) , the employer has a legal obligation to ensure that the workplace is safe and without risks to health (Section 21). This means identifying whether there are any hazards associated with electrical equipment, assessing the associated risks and taking measures to eliminate or control those risks.
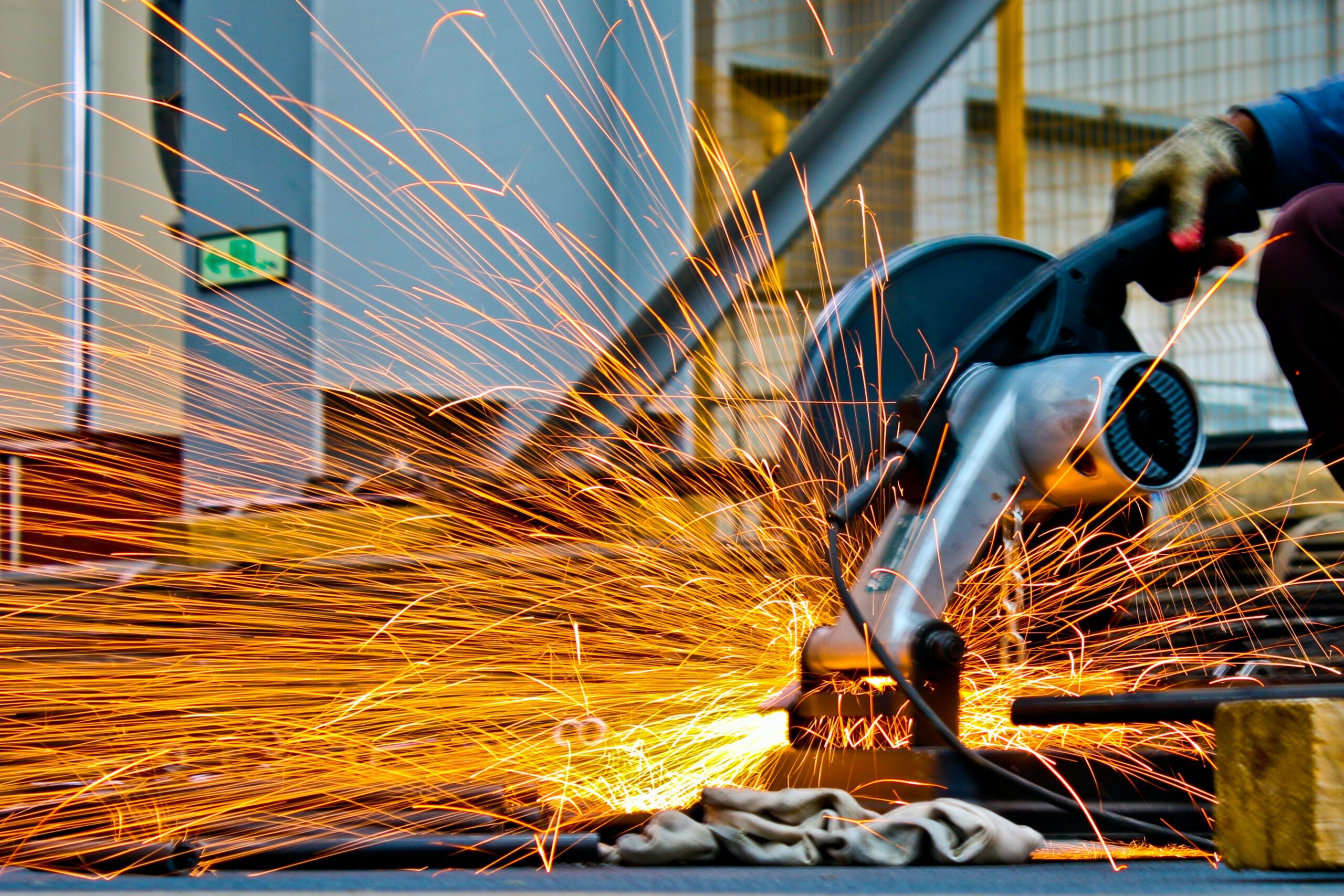
Put Safety First
Inspecting and testing electrical equipment will help determine whether it is electrically safe.
Regular visual inspection can identify obvious damage, wear or other conditions which might make electrical equipment unsafe. Many electrical defects are detectable by visual inspection for example, damaged cords.
Regular testing can detect electrical faults and deterioration that cannot be detected by visual inspection.
The nature and frequency of inspection and testing depends on factors such as the nature of the electrical equipment, how it is used and its operating environment.
The WHS Regulations have specific requirements for electrical equipment used in a ‘hostile operating environment’.
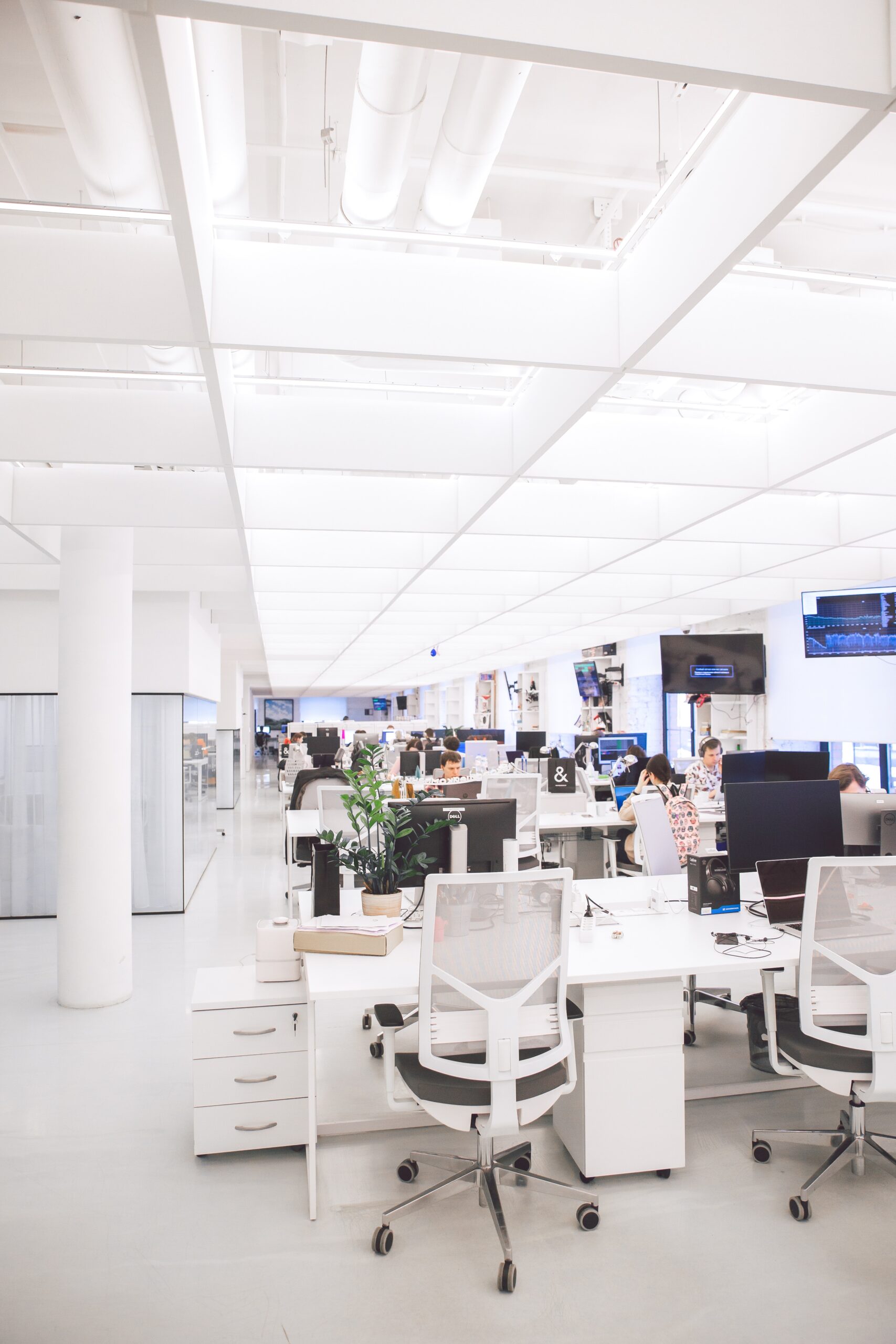
Examples Of Appliances for Test &Tagging
Laptop Computers
Desktop computers and monitors
Printers
Photocopiers
Fax machines
Staff kitchen & tea room appliances
All electric power tools
Extension cords
Power boards
IEC Leads
All double insulated appliances
Audio/visual equipment
Portable air conditioners
Isolation transformers
Desk lamps
Vacuum cleaners and electrical cleaning equipment
Fork lift chargers
3 phase electrical equipment
RCD’s – Safety Switch